PCBA Khusus 2 Lapis Berkualitas Tinggi Khusus untuk Konektor
Info dasar
Model nomor. | PCBA-A48 |
Metode perakitan | Pasca Pengelasan |
Paket transportasi | Kemasan anti-statis |
Sertifikasi | UL, ISO9001&14001, SGS, RoHS, Ts16949 |
Definisi | IPC Kelas2 |
Spasi/Garis Minimal | 0,075mm/3mil |
Aplikasi | Transmisi sinyal |
Asal | Buatan China |
Kapasitas produksi | 720.000 M2/Tahun |
Deskripsi Produk
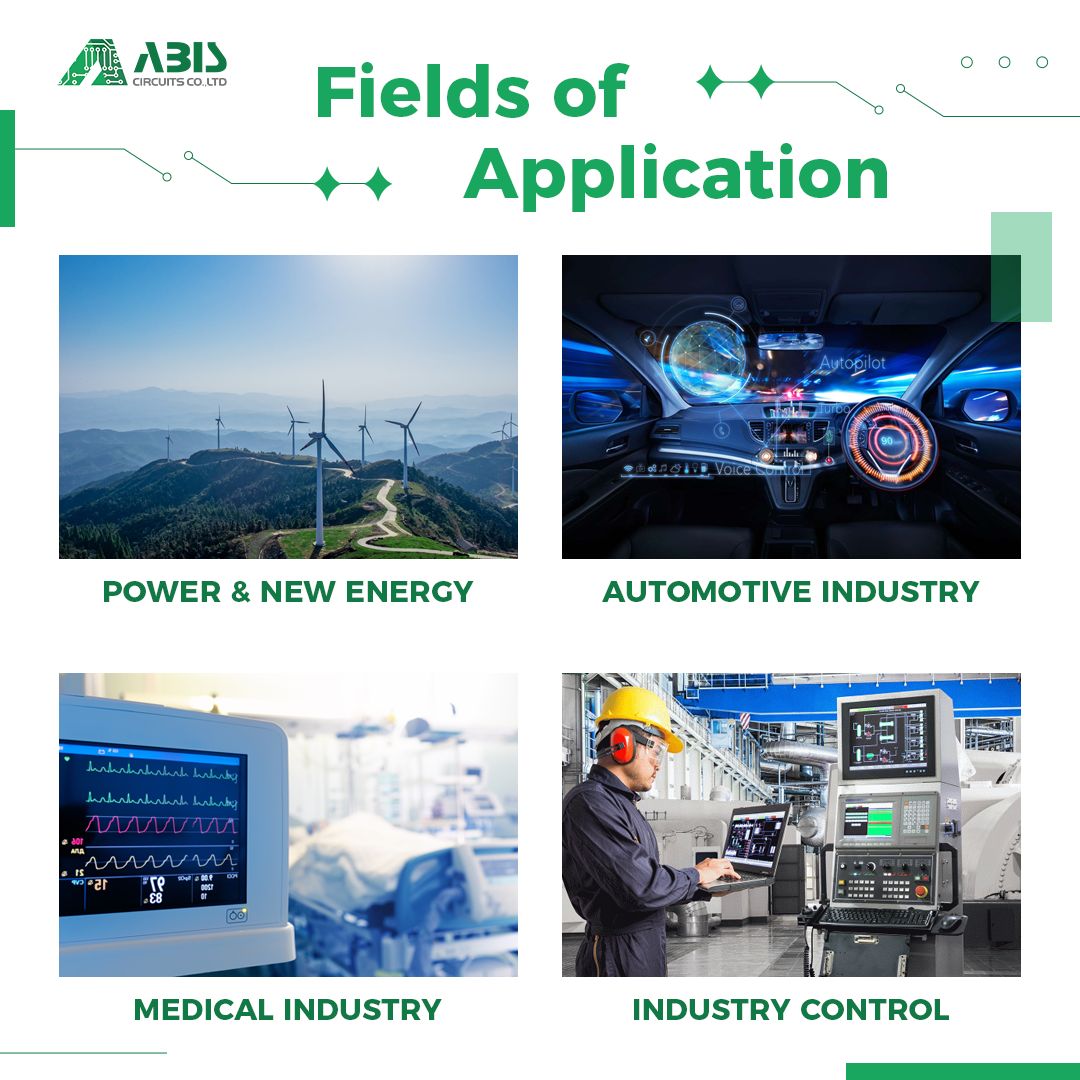
Kemampuan PCBA
1 | Perakitan SMT termasuk perakitan BGA |
2 | Chip SMD yang diterima: 0204, BGA, QFP, QFN, TSOP |
3 | Tinggi komponen: 0,2-25mm |
4 | Pengepakan minimal: 0201 |
5 | Jarak minimum antar BGA : 0,25-2,0mm |
6 | Ukuran minimum BGA: 0,1-0,63mm |
7 | Ruang QFP minimum: 0,35 mm |
8 | Ukuran perakitan minimum: (X*Y): 50*30mm |
9 | Ukuran perakitan maksimal: (X*Y): 350*550mm |
10 | Presisi penempatan pengambilan: ±0,01mm |
11 | Kemampuan penempatan: 0805, 0603, 0402 |
12 | Tersedia press fit dengan jumlah pin tinggi |
13 | Kapasitas SMT per hari: 80.000 poin |
Kemampuan - SMT
Garis | 9(5Yamaha,4KME) |
Kapasitas | 52 juta penempatan per bulan |
Ukuran Papan Maks | 457*356mm.(18”X14”) |
Ukuran Komponen Minimal | 0201-54 mm persegi.(0,084 inci persegi), konektor panjang, CSP,BGA,QFP |
Kecepatan | 0,15 detik/chip, 0,7 detik/QFP |
Kemampuan - PTH
Garis | 2 |
Lebar papan maks | 400 mm |
Jenis | Gelombang ganda |
status pbs | Dukungan saluran bebas timah |
Suhu maks | 399 derajat C |
Semprotkan fluks | tambahan |
Memanaskan lebih dulu | 3 |
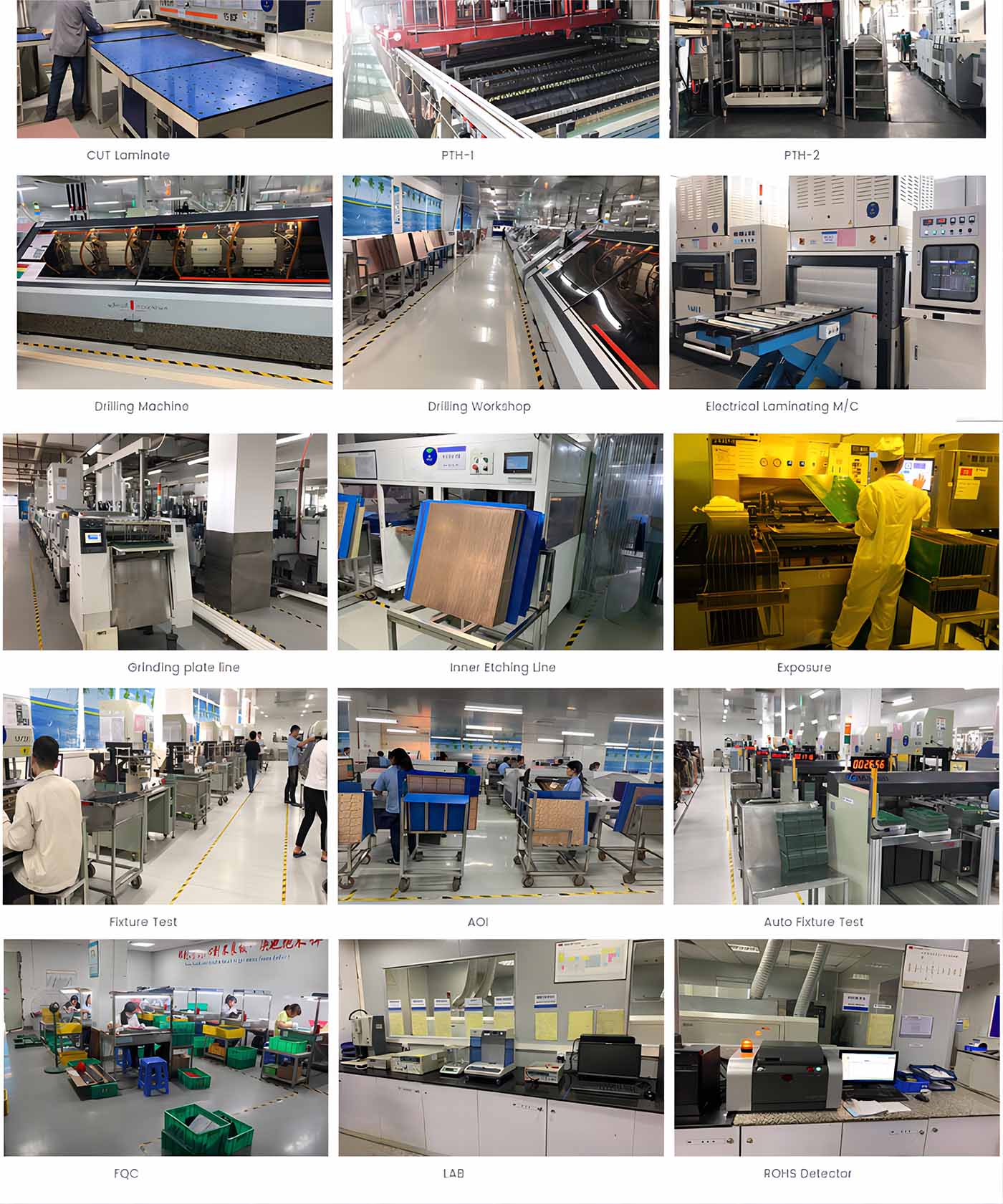
Waktu Pimpin Q/T
Kategori | Waktu Pimpin Tercepat | Waktu Pimpin Biasa |
Dua sisi | 24 jam | 120 jam |
4 Lapisan | 48 jam | 172 jam |
6 Lapisan | 72 jam | 192 jam |
8 Lapisan | 96 jam | 212 jam |
10 Lapisan | 120 jam | 268 jam |
12 Lapisan | 120 jam | 280 jam |
14 Lapisan | 144 jam | 292 jam |
16-20 Lapisan | Tergantung pada persyaratan spesifik | |
Di atas 20 Lapisan | Tergantung pada persyaratan spesifik |
Kontrol kualitas
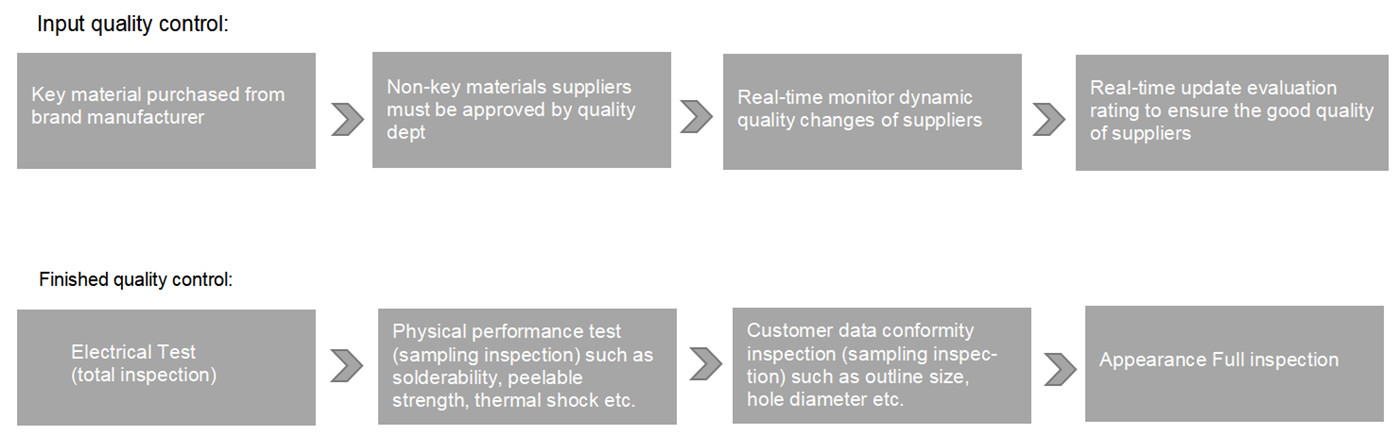
Pengujian AOI | Periksa pasta solder. Periksa komponen hingga 0201 Memeriksa komponen yang hilang, offset, bagian yang salah, polaritas |
Pemeriksaan Sinar-X | X-Ray menyediakan pemeriksaan resolusi tinggi untuk: BGA/BGA Mikro/paket skala Chip/Papan Telanjang |
Pengujian Dalam Sirkuit | Pengujian In-Circuit biasanya digunakan bersama dengan AOI untuk meminimalkan cacat fungsional yang disebabkan oleh masalah komponen. |
Tes Penyalaan | Pemrograman Perangkat TestFlash Fungsi Lanjutan Pengujian fungsional |
- Inspeksi masuk IOC
- Inspeksi pasta solder SPI
- Inspeksi AOI online
- Inspeksi artikel pertama SMT
- Penilaian eksternal
- Inspeksi pengelasan X-RAY
- Pengerjaan ulang perangkat BGA
- inspeksi QA
- Pergudangan dan pengiriman anti-statis
Pertanyaan Umum
A:
Bill of material (BOM) merinci:
A),Mnomor bagian pabrikan,
B),Cnomor suku cadang pemasok komponen (misalnya Digi-key, Mouser, RS )
c), foto sampel PCBA jika memungkinkan.
d), Kuantitas
A:Sampel gratis tergantung pada jumlah pesanan Anda.
A:
Tidak, kami tidak dapat menerima file gambar, jika Anda tidak memiliki file gerber, dapatkah Anda mengirimkan sampel kepada kami untuk disalin.
Proses Penyalinan PCB & PCBA:
A:
Prosedur Penjaminan Mutu kami seperti di bawah ini:
a), Inspeksi Visual
b), Probe terbang, alat perlengkapan
c), Kontrol impedansi
d), Deteksi kemampuan solder
e), Mikroskop metalografi digital
f),AOI(Inspeksi Optik Otomatis)
A:Silakan kirimkan pertanyaan detail kepada kami, seperti Nomor Barang, Jumlah setiap barang, Permintaan kualitas, Logo, Ketentuan Pembayaran, Metode transportasi, Tempat pembuangan, dll. Kami akan membuatkan penawaran harga yang akurat untuk Anda sesegera mungkin.
A:Setiap Pelanggan akan memiliki penjualan untuk dihubungi dengan Anda.Jam kerja kami: AM 9:00-PM 19:00 (Waktu Beijing) dari Senin sampai Jumat.Kami akan membalas email Anda sesegera mungkin selama waktu kerja kami.Dan Anda juga dapat menghubungi sales kami melalui ponsel jika mendesak.
A:Ya, kami dengan senang hati menyediakan sampel modul untuk menguji dan memeriksa kualitas, pesanan sampel campuran tersedia.Harap dicatat pembeli harus membayar biaya pengiriman.
A:ya, Kami memiliki tim insinyur gambar profesional yang dapat Anda percayai.
A:Ya, kami memastikan bahwa setiap bagian PCB, dan PCBA akan diuji sebelum pengiriman, dan kami memastikan barang yang kami kirim dengan kualitas yang baik.
A:Kami menyarankan Anda menggunakan pengirim DHL, UPS, FedEx, dan TNT.
A:Melalui T/T, Paypal, Western Union, dll.